6. Изнашивание режущего клина
6.1. Виды изнашивания и меры износа.
Во время резания происходит изнашивание режущего клина, проявляющееся по-разному - в зависимости от вида и длительности нагрузки. На рис.21 показаны наиболее часто встречающиеся виды изнашивания токарного резца. Режущий клин изнашивается по передней поверхности (лункообразный износ) и по задней поверхности - (маркировочная ширина площадки износа); оксидный (окислительный) износ на вспомогательной задней поверхности имеет второстепенное значение. Два первых вида изнашивания принимаются в качестве критериев стойкости.
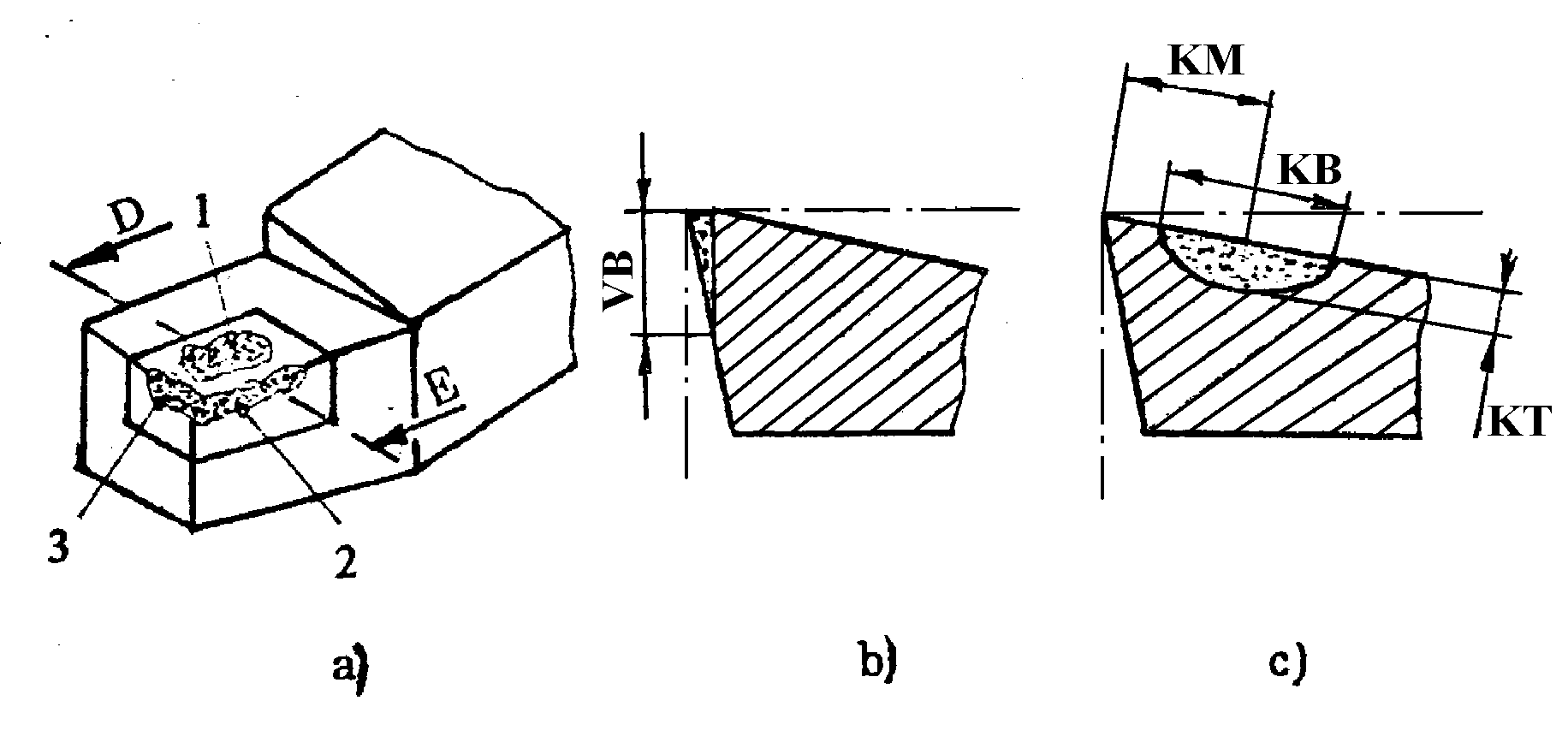
Рис.21. Виды изнашивания и меры износа
Меры износа показаны на рис. 21b,c. Различают ширину площадки износа VB, измеренную в миллиметрах (рис. 21b) на задней поверхности режущего инструмента, и соотношение K размеров лунки, определяемое отношением глубины лунки KT к положению середины лунки KM.
Вследствие сложности процессов трения в контактных зонах инструмента и в результате действия чрезвычайно высоких механических и термических нагрузок происходит быстрый износ инструмента. Можно привести следующие основные причины, вызывающие интенсивное изнашивание:
- повреждение режущей кромки, происходящее вследствие механических и термических перенапряжений;
- адгезия (срез на местах схватывания под нагрузкой);
- диффузия и механическое изнашивание;
- тепловое изнашивание (угорание металла).
Эти процессы в сильной степени накладываются один на другой и могут лишь частично рассматриваться самостоятельно с точки зрения как причин, их вызывающих, так и проявления процесса.
6.2. Причины изнашивания
Повреждение режущей кромки. Повреждения режущей кромки, такие, как сколы, продольные и поперечные трещины или пластические деформации, наступают при механических или термических перегрузках.
Сколы. Большие силы резания вызывают сколы на режущей кромке или на вершине резца в том случае, когда либо угол клина или угол при вершине инструмента слишком малы, либо используется слишком хрупкий режущий материал. При таких повреждениях положение плоскостей скола определяется направлением силы резания. Сколы могут быть вызваны также прерывистым резанием, прежде всего при обработке вязких материалов, когда образуется налипающая на режущем клине стружка. Небольшие сколы появляются тогда, когда заготовки имеют твердые неметаллические включения, возникающие при дезоксидации стали. К перенапряжениям такого рода очень чувствительны износостойкие сорта твердых сплавов, особенно, если инструмент из этих материалов работает при относительно малом поперечном сечении стружки (развертывание, шабрение).
Поперечные трещины. При прерывистом резании (например, при фрезеровании) на режущую кромку действуют изменяющиеся нагрузки, что может привести к сколам. Кратковременные изменения силы резания приводят к появлению поперечных трещин, характерных для фрезерования. Быстроменяющиеся нагрузки в процессах, для которых характерна суставчатая стружка, могут также при превышении критического количества циклов нагружения привести к образованию поперечных трещин.
Продольные трещины. Термические напряжения при прерывистом резании вызывают повреждение режущей кромки инструмента, при котором краткосрочные изменения температуры приводят к образованию продольных трещин. Характер продольных трещин совпадает с линиями изотерм температурного поля в режущем клине. При фрезеровании режущая кромка нагревается до высокой температуры, а потом остывает на воздухе. Напряжения растяжения в поверхностных слоях могут превысить предел текучести, который для нагретого инструмента меньше, чем для холодного, что приводит к пластическим деформациям. Пластические деформации возможны в инструментальных сталях при несквозной закалке и в твердых сплавах с высоким содержанием связок, или когда температура режущей кромки вырастает настолько, что материал режущей части размягчается.
Механическое изнашивание. Изнашиванием называется отрыв частиц режущего материала, которые уносятся под влиянием внешних сил. Причиной изнашивания могут служить твердые включения в материале, такие, как карбиды и оксиды.
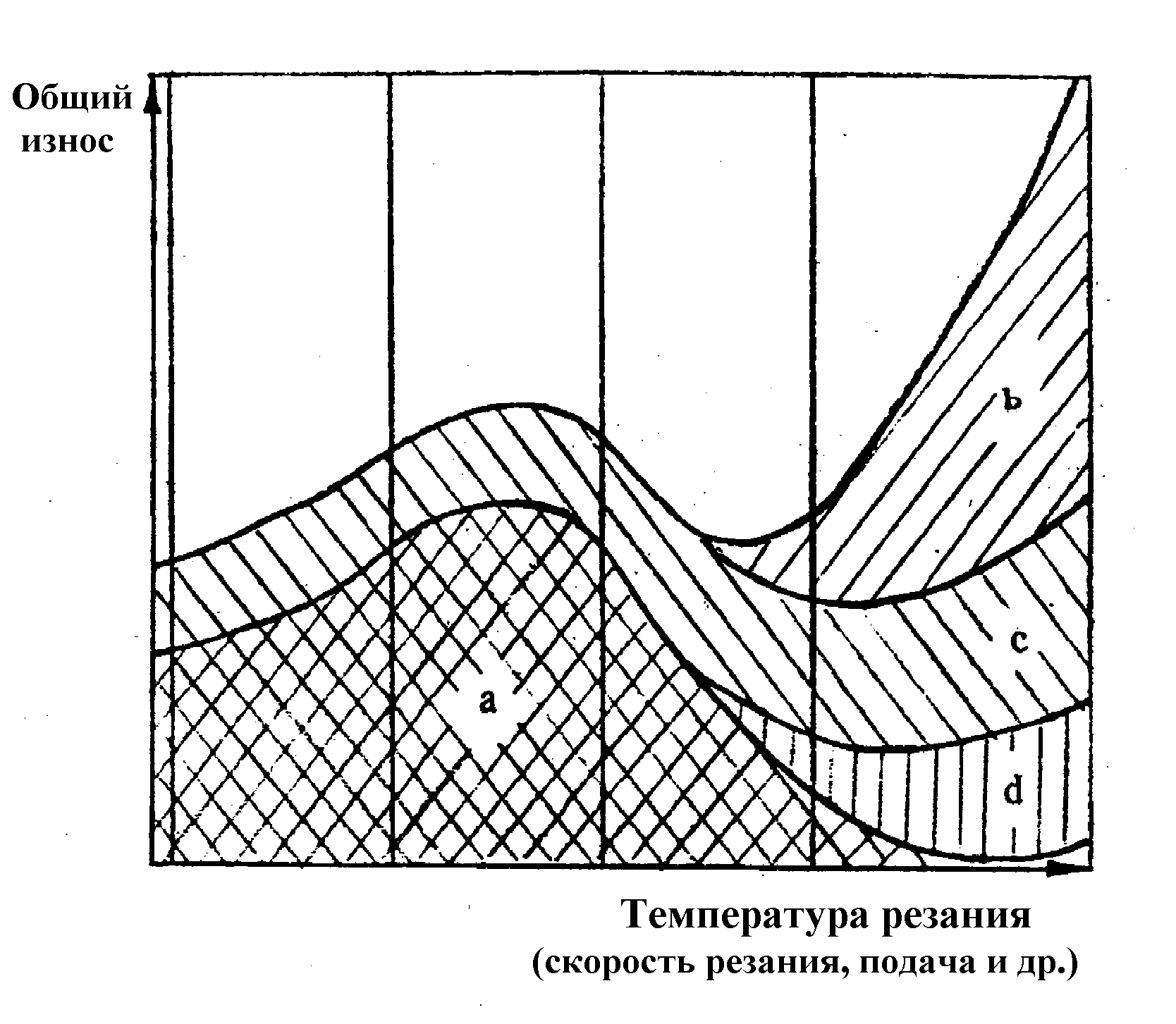
а) скалывание, b) диффузионные процессы, c) механическое изнашивание, d) тепловое изнашивание
Адгезия. Изнашивание посредством сваривания под давлением возникает вследствие того, что под влиянием свободных силовых полей при достаточно сближенных свободных от оксидов поверхностях происходит их сваривание. Прочность сварных мест тем выше, чем больше деформация. Во время стружкообразования те слои материала, которые образуют граничный слой между передней поверхностью инструмента и стружкой сразу после ее отделения пластически сильно деформированы. Поэтому материал стружки и особенно ее, вновь возникшие, поверхности вследствие их нагрева, деформирования и свежих разрывов находятся в активном состоянии. Повышенный износ, обусловленный таким схватыванием (свариванием), наблюдается при большой шероховатости поверхностей инструмента, прерывистом контакте между заготовкой и инструмента, а также при прерывании схода материала по рабочим поверхностям инструмента. Такой вид изнашивания характерен для низких скоростей резания и интенсивном наростообразовании. Многочисленные эксперименты показали, что износ по задней грани с увеличением скорости резания растет не непрерывно, а имеет, по крайней мере, два экстремальных значения. Сначала износ достигает максимума на скорости, при которой нарост достигает наибольшего значения. Уменьшение величины износа наступающее на скорости, при которой нарост исчезает, связано с увеличением температуры в зоне контакта инструмент-стружка-деталь и, связанных с этим, повышением пластичности контактных слоев обрабатываемого материала и снижением сил трения, действующих на поверхности инструмента.
Диффузия. Твердосплавные инструменты, обладающие повышенной склонностью к тепловому изнашиванию и работающие при высоких скоростях резания подвергаются диффузионному изнашиванию. Инструментальные и быстрорежущие стали размягчаются при температуре, когда диффузия едва ли может проявляться (например, около 6000С для быстрорежущей стали). Для подавления диффузионной реакции в твердые сплавы включают малочувствительные к такой реакции компоненты (например, карбид титана).
Тепловое изнашивание. При визуальном наблюдении инструмента после процесса резания вблизи контактной зоны можно заметить цвета побежалости, что свидетельствует о тепловом изнашивании (процессе оксидирования режущего материала). Тепловое изнашивание изменяется в зависимости от легирующих присадок режущего материала и температуры резания. Твердый сплав начинает терять свои режущие свойства уже при температурах 700-8000С, причем, твердые сплавы из карбида вольфрама и кобальта (группы WC+Co) окисляются сильнее, чем такие же, но с присадками карбида титана или других карбидов (TiC+WC+Co, TaC+TiC+WC+Co). Для инструментальных и быстрорежущих сталей тепловое изнашивание можно не учитывать, так как их теплостойкость меньше температуры, при которой начинается сильное оксидирование поверхности.
6.3. Период стойкости
При оценке обрабатываемости материала и режущей способности режущего инструмента различают четыре основных оценочных величины период стойкости инструмента: силу резания, определяемую в соответствии со стандартом ДИН 6584, шероховатость поверхности обработанной заготовки по ДИН 4760 и условия стружкообразования. Для характеристики обрабатываемости одновременно используют несколько оценочных величин, но в общем случае предпочтительнее период стойкости инструмента.
Период стойкости Т - это время (в мин),течение которого инструмент может производить резание, т.е. время от начала работы инструмента до прихода его в состояние невозможности дальнейшего использования, которое определяется по заданному критерию стойкости или для неперетачиваемых инструментов - до их замены. Обычно принимают Т = 45,,,60 мин.
В зависимости от способа обработки для оценки стойкостных возможностей инструмента используются и другие показатели стойкости: путь резания, проходимый инструментом по обрабатываемой поверхности; число деталей, обработанных за период стойкости; площадь обработанной поверхности или объем стружки, полученные за тот же период.
Путь L за период стойкости - это путь, который инструмент или режущая кромка могут пройти до достижения выбранного критерия стойкости (например, для оценки стойкости сверл). В отношении движений необходимо различать путь за период стойкости в направлении действительного движения резания и движения подачи.
Стойкость можно определить числом обработанных заготовок или рабочих операций, после выполнения которых инструмент или его режущая кромка достигают выбранного критерия стойкости.
Обычно период стойкости устанавливается: по справочной литературе; принудительно, как правило, в зависимости от цикла обработки или с целью повышения производительности (например, подачи); экспериментальным путем.
Экспериментальное определение периода стойкости. В этом случае в течение долгого времени проводятся эксперименты по определению точных значений периодов стойкости для наиболее часто встречаются условия резания. В связи с большим расходом материалов и затратами времени эти эксперименты проводят преимущественно для условий массового производства. Результаты исследований служат основной для определения оптимальных условий резания.
Ограниченные эксперименты проводят для определения относительных исходных значений обрабатываемости материалов, при обеспечении возможности их минимального расхода и уменьшения затрат времени. Характеристика таких опытов не позволяет сделать прямых заключений относительно периода стойкости инструмента. Их используют, как исходные контрольные значения для обрабатываемых и обрабатывающих материалов, а также для проверки обрабатываемости.
Определение стойкости по температуре. Опыты по температурному определению периода стойкости инструмента служат для установления времени, в течении которого инструмент в состоянии проводить работу резания при определенных условиях. Характеристикой температурного периода стойкости является потеря кромкой режущей способности, т.е. ее переход в состояние, когда существует чистое трение.
Определение периода стойкости по износу. Такие эксперименты проводятся в тех случаях, когда к потере режущей способности инструмента приводит не изменение температуры резания, а, в первую очередь, износ инструмента. Инструменты из твердых сплавов и быстрорежущих сталей, работающие при высоких скоростях резания в большинстве случаев имеют одинаковый износ по передней и задней граням, который ограничивает период стойкости инструмента. В опытах по определению периода стойкости токарного инструмента по его износу при продольном точении с постоянной скоростью резания предусмотрено измерение износа на задней и передней поверхностях инструмента через различные промежутки времени. В общем случае достаточно определить ширину VB площадки износа на задней грани, глубину KT лунки и расстояние KM от середины лунки износа до режущей кромки (рис. 23). При этом в зависимости от продолжительности резания для четырех различных скоростей резания (с заданной разностью между ними) определяют увеличения ширины площадки износа, а также изменения положения середины лунки.
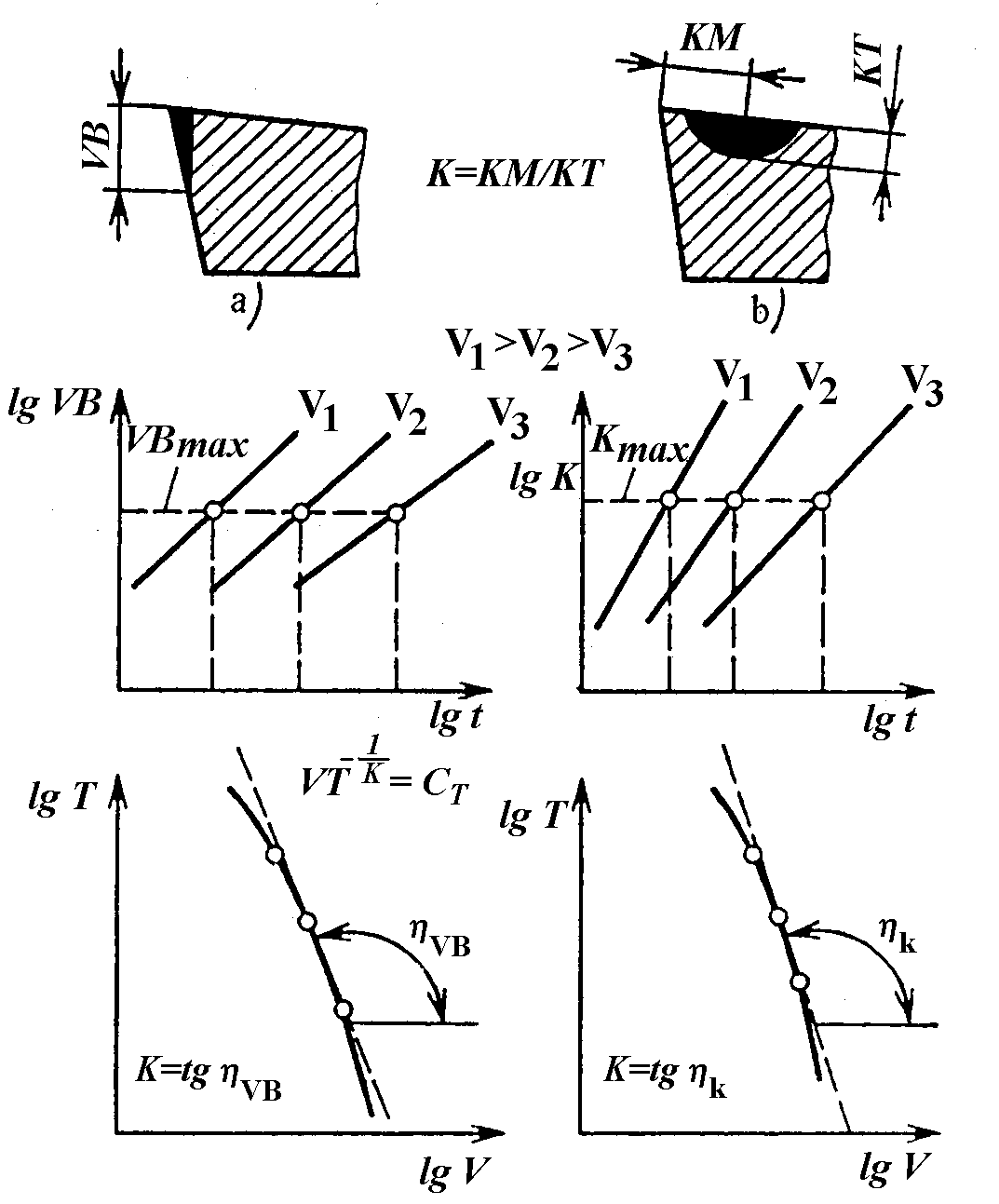
Рис.23. Меры очагов износа: а) износ по задней грани, б) лункообразный износ
Для графического представления результатов измерения целесообразно использовать двойные логарифмические координаты, где по оси абсцисс откладывается время резания t (мин), по оси ординат ширина VB площадки износа или соотношением размеров лунки к=КТ/КМ. Для постоянной скорости резания измеренные значения располагаются приблизительно по прямой (рис. 23). При этом характеристиками являются: а) скорость резания для определенного периода стойкости (например, 20, 30 или 60 мин) и износа (например, VB=0,2 мм, K=0,1 или KT=0,1 мм),т.е. скорость резания, при которой через период стойкости, равны, например, 30 мин ширина площадки износа достигает VB=0,2 мм; б) два уравнения для видов изнашивания, ширина площадки износа или глубины лунки износа прямолинейного участка кривой: vT exp (-1/v) = CT причем должны быть указаны значения для (-1/v) и CT.
По кривым можно сделать заключение о влиянии времени и скорости резания на износ и режущую способность инструмента при обработке различных материалов. В общем случае кривые лункообразного износа идут круче, чем кривые износа по задней поверхности.
Обычно для быстрорежущей стали v = -(7-12), для твердых сплавов v= -(2-6), а для минералокерамики v = -(1,5-3).